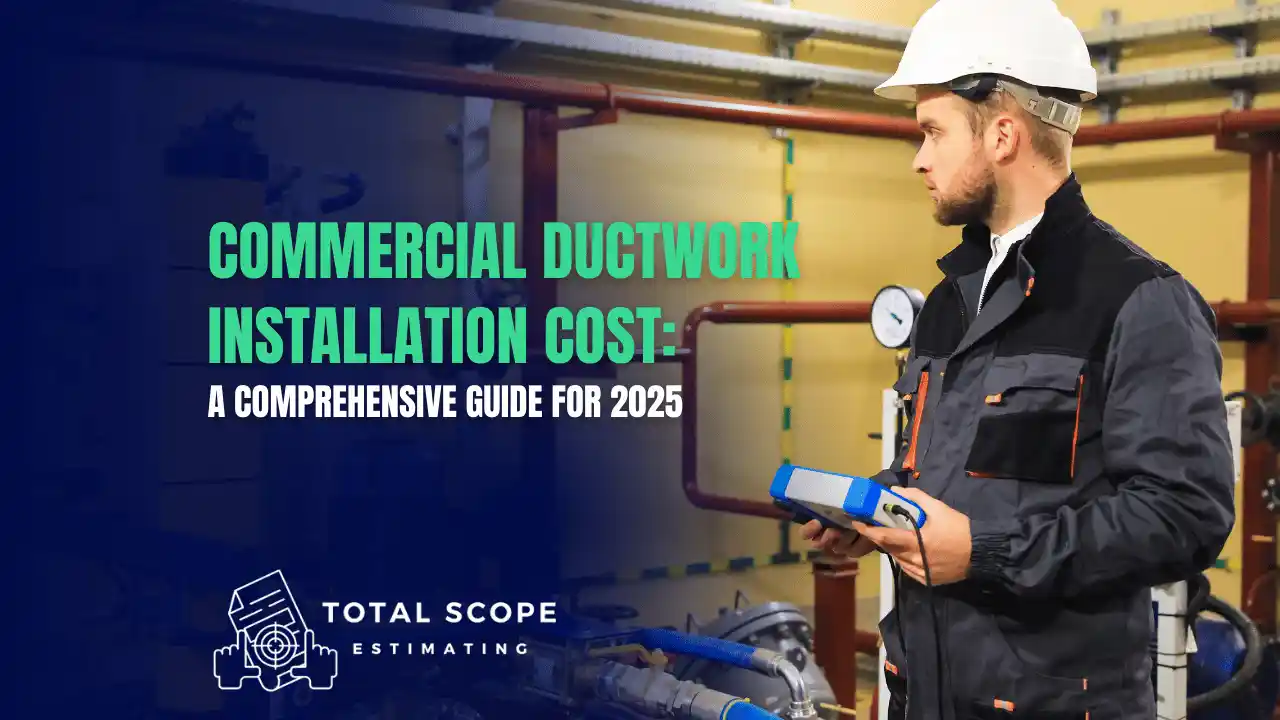
A well-built HVAC ( Heating, Ventilation, and Air Conditioning ) system is essential for sustaining a comfortable environment and confirming air quality. Ductwork is the foundation of this system, providing heated or cooled air throughout the building. The commercial ductwork installation cost is vital for budget planning and successful project execution, whether you are designing a new construction or modifying an existing space.
In 2025, many factors, from the building size to the type of materials used, labor rates and other integrants such as insulation and zooming system, affect commercial ductwork installation costs. In this article, we’ll be surveying these factors in detail, helping you make instructed decisions and proposals for a successful ductwork installation.
Understanding the Scope of Commercial Ductwork Installation
Before considering the specific costs, it is necessary to have a clear picture of the requirements for commercial ductwork installation. Occasionally, this process involves plotting and installing a web of ducts that deliver air from the HVAC system to different building sectors. These ducts are made of sheet metal, fiberglass, or flexible ducting. They must be installed according to building codes and HVAC industry standards.
The complexity of commercial ductwork installation depends on several factors, such as the layout and size of the building, the number of zones or rooms that demand air distribution, and the HVAC system’s capacity. A larger building with complex zoning requirements will naturally require a more intricate and costly ductwork system than a more straightforward and smaller space.
If you are looking for professional commercial plumbing or ductwork estimating services near you, vist this page.
Factors That Influence the Commercial Ductwork Installation Cost
Many key factors regulate the overall Commercial Ductwork Installation Cost in a commercial building. Knowing these factors will help you understand the outlay in detail and plan your budget accordingly.
1. Size of the Building
It is the most crucial factor that influences the Commercial Ductwork Installation Cost. A huge ductwork system is required for more significant buildings to evenly distribute air across all areas. The amount of ductwork varies according to the demand for square footage as it increases the amount of material and labor cost increases.
For example, an ample retail space, hospital, or industrial facility will require a more complicated network of ducts to support multiple floors, zones, and specialized areas like clean rooms or kitchens than a small office space that demands simple or basic ductwork systems.
2. Type of Ductwork Material
The type of material used for the ducts plays a vital role in determining the overall cost of the installation. Various kinds of materials are commonly used in commercial ductwork, each with its cost range and advantages:
- Sheet Metal Ducts: The most common material used for commercial ductwork is sheet metal galvanized by steel and aluminum. The properties that make it ideal for large commercial buildings are its durability, resistance to moisture and molds, and long-running. However, these ducts tend to be more costly due to the expenses of material and the labor required for installation.
- Flexible Ducts: Flexible ducts made from a wire coil sheeted in a flexible plastic material are typically used in areas where space is limited or rigid ducts are difficult to install. They are cheaper and easier to install than sheet metal. They are not as long-lasting and may require substitution sooner.
- Fiberglass Ducts: These ducts, lined with fiberglass insulation, lined with fiberglass insulation, are commonly used in commercial buildings to ensure energy efficiency and noise reduce. Fiberglass ducts are more expensive than flexible ducts, but they can provide long-term savings on energy costs.
Material costs will rise and fall in 2025 due to global supply chain dynamics. Therefore, it is crucial to be updated before finalizing your estimate.
3. Labor Costs
Labor is another significant component of the total cost of ductwork installation. In 2025, the labor cost will be determined by geographical location, the installation’s complexity, and the HVAC contractor’s awareness.
Skilled technicians familiar with HVAC systems, building codes, and regulations are required to install ductwork in a commercial building. They must ensure that the ducts are properly insulated, sealed and positioned to increase the effectiveness and prevention of air leakage.
Labor costs are typically charged on the duration of work more complex and large projects require more work hours to decide the total price. On average, it ranges from $50 to $150 per hour, depending on the scope and region of the project.
4. Complexity of the HVAC System
The cost of ductwork installation depends on the complexity of the HVAC system. Features like zoning controls, air purification systems, and energy recovery ventilators are considered in the HVAC systems of commercial buildings rather than residential properties. Modifying these components in the existing system increases the installation cost further.
Zoning systems are standard in commercial buildings and allow precise temperature control in different areas and zones. Installation of this system demands special ductwork, including dampers and sensors, which further increases the overall cost.
5. Insulation and Sealing
To maximize energy efficiency and prevent air leakages, it is essential to have the proper insulation and sealing of the ductwork system. Otherwise, poorly sealed ducts can lead to significant energy loss, resulting in higher bills and less efficient HVAC systems.
Energy efficiency will remain a top priority for commercial building owners in 2025. Many ductwork installations now include advanced insulation to reduce heat transfer and maintain a consistent temperature. Although it can add to the upfront cost, the long-term savings on energy bills make it a beneficial investment.
6. Permits and Building Codes
Commercial ductwork installations must agree to the local building codes and regulations. It is necessary to obtain the permits, whose cost varies with location to start a project. Further, it must be inspected to ensure the safety standards and proper ductwork installation.
The cost of permits and inspections should be factored into your overall budget. Failure to comply with local regulations can lead to fines or delays in the project.
Estimating Commercial Ductwork Installation Costs
To provide a ballpark figure for commercial ductwork installation costs, consider the following average price ranges based on current market trends in 2025:
- Material Costs: According to the type of material used, you can expect to pay between $6 and $12 per linear foot for sheet metal ducts, $3 to $6 per linear foot for flexible ducts, and $8 to $15 per linear foot for insulated fiberglass ducts.
- Labor Costs: Labor costs commonly range from $50 to $150 per hour, depending on the complexity of the installation and the contractor’s experience. A small commercial project may require a few days to complete, while more extensive or more complex installations could take several weeks.
- Total Costs: On average, the total cost for installing ductwork in a small to mid-sized commercial building can range from $8,000 to $20,000, depending on the abovementioned factors. For more significant buildings or projects requiring more advanced HVAC systems, the cost can exceed $50,000.
Additional Costs to Consider
In addition to the primary costs associated with ductwork installation, other potential expenses should be considered:
- Duct Cleaning and Maintenance: After the completion of installation, regular cleaning and maintenance are crucial to keep the ducts working correctly. With the passage of time, dust, dirt, and debris can aggregate in the ducts, reducing the efficiency of the HVAC system and impacting indoor air quality.
- Upgrades for Energy Efficiency: In 2025, the demand for energy-efficient HVAC systems is increasing due to the rising cost of energy and sustainability concerns. The upgradation of energy-efficient ductwork and the addition of features like zone controls and smart thermostats increase the price but reduce the saving concerns.
- Repairs and Modifications: You may have a need to make the repairs and changings to the current ductwork system if you’re retrofitting an existing building. It includes replacing damaged ducts, leakage, sealing, or upgrading insulation, which will be calculated in the total cost.
Conclusion
The Commercial Ductwork Installation Cost can vary widely depending on the size of the building, the materials used, labor rates, and the complexity of the HVAC system. By knowing the key factors that affect these costs and planning accordingly, you can ensure that your ductwork installation project is completed on time and within budget.
Staying current with industry trends, material costs, and technological advancements is essential for accurately estimating costs in 2025. Whether you’re building a new commercial space or upgrading an existing one, working with an experienced HVAC contractor and investing in quality materials will ensure your ductwork system is well-planned, reliable, and built to last.
For more detailed estimates and assistance with commercial ductwork installation projects, Total Scope Plumbing Estimator offers detailed estimating services according to your needs. Reach out to our team for a personalized consultation and ensure the progression of your project from start to finish.